|
Manufacturing of pellets directly from powder.
|
|
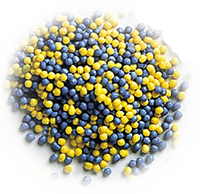 |
Effective process. Pellets are manufactured directly from powder with
a binder or solvent. Fast process. Low usage of auxiliary materials.
|
Product advantages. Compact, round pellets - ideal for automatic
dosing and even coating.
|
Comparison. Pellets have a higher density than spray granulates and
agglomerates.
|
|
Pellet diameter. Between ca. 0.2mm and
1.2mm.
|
|
Process Principles
|
|
|
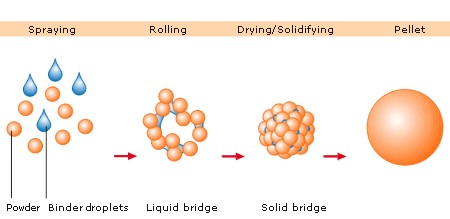
|
|
Powder is mixed and moistened. A solvent or binder can also be added. The
powder bed is set into a centrifugal motion. (-> Fluid Bed Pelletizing in the rotor). The impact
and acceleration forces that occur in this process result in the formation of
agglomerates, which become rounded out into uniform and dense pellets. The speed
of rotation has a direct influence on the density and size of the
pellets. The moist pellets are subsequently dried in the fluid bed. If
required, the systems can be made inert for applications with organic
solvents. Another alternative for direct pellitizing is Spray Granulation.
|
|
Product characteristics of the pellets
|
|
Round pellets
Good flow behaviour
Easy to dose
Good dispersibility
Compact structure
High bulk density
Dense surface
Wide grain diameter spectrum
Low abrasion
|
With suitable additives, pellets can be made into tablets or used to fill
capsules. The round shape is ideal for uniform coating. Pellets are good for
automatic dosing.
|
|
Manufacturing options
For this process, Glatt offers systems with different capacities: Batch Fluid Bed Systems with
batch sizes from 500g to 250kg/batch. Continuous Fluid Bed Systems with
throughputs from 10kg/h to 0.5t/h. |
|
|
|